Concrete has transformed the world. It is durable, adaptable, resilient, and affordable, so it is not surprising that it is the building industry’s material of choice. Unfortunately, it is also a huge source of carbon emissions and, left unchecked, threatens to wreak havoc on the environment. Metabolic’s green building consultant Nico Schouten examines the pros and cons of concrete and explains why it is not too late to make different choices.
2050: Future development
When I open my window in the year 2050, there is a great chance that no matter where I am in the world, I will look out onto a city. This future city is not made of slabs of grey, drab concrete. I envision a sustainable environment, with lush green plants growing everywhere, a place where people live comfortably and enjoy a healthy lifestyle. And this can be the case, but only if we rethink how we are building today.
2021: How and why concrete is so ever-present in our lives
Concrete is quite literally the foundation of our modern civilization. It is relatively cheap, strong, made from resources that we (seemingly) have an abundance of, can take many shapes, and has a very long lifespan. First used by the Romans to create buildings such as the Pantheon and the Colosseum, concrete became the go-to building material in Europe after the Second World War because of the huge demand for cheap housing. But as we produce more and more concrete, compounding environmental issues are cause for concern. We will explore how using more sustainable materials and design strategies could alleviate the impacts of the construction sector.
The UN has predicted that more than 66% of us will live in a concrete jungle by 2050. We are seeing a radical shift to megacities, which have a population of more than 10 million people, with 33 megacities identified in 2020 and a predicted six more by the end of the decade. At this rate, we will have to build 2 billion new homes before the end of the 21st century. That is like adding eight New York City’s every year.
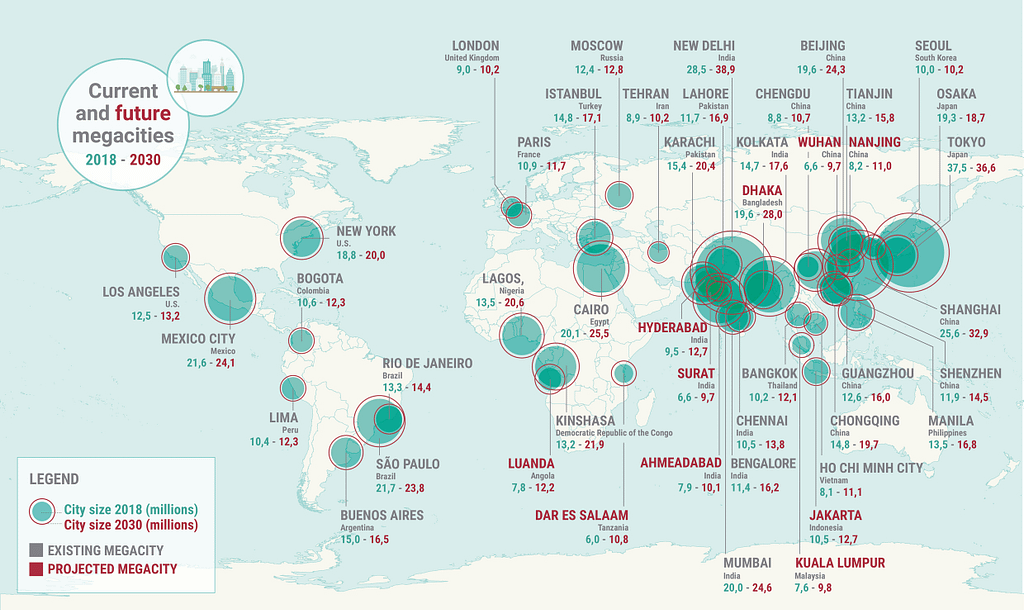
It is very likely that we will build these homes with concrete, the most used building material in the construction sector. We use more than twice as much concrete as all other building materials combined. This makes it the second most used material in the world (after water) and the most consumed man-made material with a staggering 10 billion tons of it produced each year. This would be enough to cover all of the UK in a 2 cm layer of concrete or to build 1,700 Hoover Dams, or 90,000 Burj Khalifas each year.
Where do we find concrete?
Think of concrete as the skeleton of a building. It is typically used for the foundation and construction, meaning the average building is roughly 80% concrete. The concrete skeleton is then clad with a facade and roof (the skin), installations such as lights and plumbing (organs), and certain finishes such as windows (the analogy is a bit harder here, but let’s say eyes). Take concrete away and the building falls apart. Using a material that is sturdy and long-lasting seems like the smart choice for the ‘skeletons’ of our homes.
The downsides of concrete
Unfortunately, there are some negative consequences to using concrete, notably, the emission of CO2 during the production process. Taking in all stages of production, concrete is responsible for 4 to 8% of the world’s CO2. Half of concrete’s CO2 emissions are created during the manufacture of clinker, the basis of cement and what binds together all the components in concrete. To make this, limestone and several chemical additives are heated to 1450 C, so it is by far the most energy-intensive part of the cement-making process. But beyond CO2, there are even more issues to be addressed.
1. Depletion of sand
It would seem that if there was one thing we have enough of in the world, it is sand. Sand is one of the main components of concrete, but unfortunately, not all types are suitable. Typically, we use sand from river beds and oceans because of the surface texture created by the corrosive workings of the water. With the increased consumption of concrete over the last century, sand is becoming a sought-after resource, which has started to affect the world around us. Regulations in the West protect the (natural) environment but other parts of the world have seen a “sand mafia” emerge.
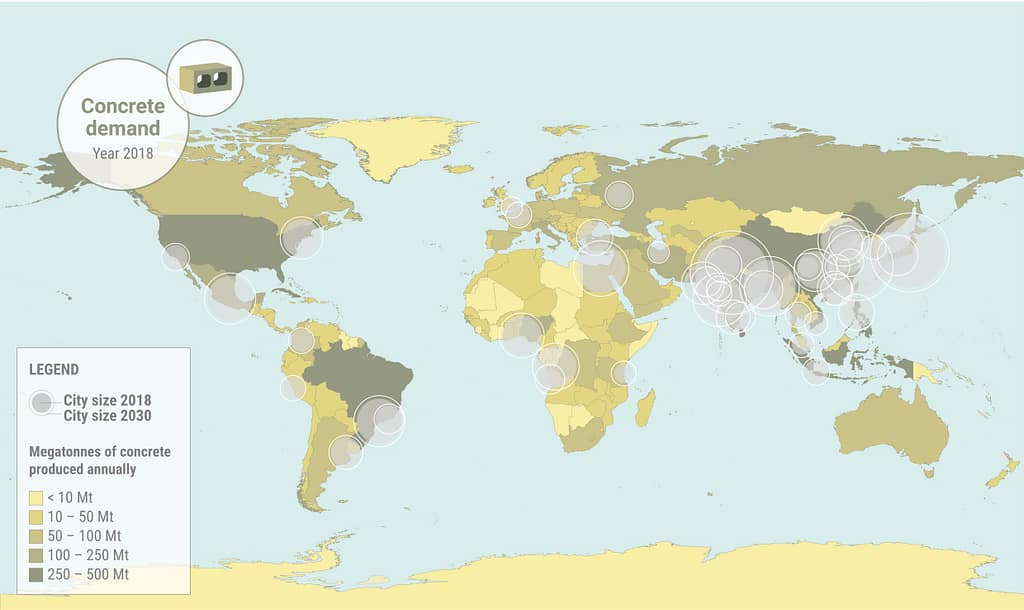
The uncontrolled taking of sand can devastate local habitats and species. In Africa, China, and Southeast Asia, where we see huge population growth, extracting sand from rivers and lakes creates standing pools of water that become breeding sites for mosquitoes carrying malaria and other emerging diseases.
The destruction of natural ecosystems is also a threat for rural communities which are largely dependent on them for their livelihoods. There are many stories of fishing communities that can no longer survive because their fishing grounds and fish-breeding estuaries have been destroyed by the dredging of sand.
The uncontrolled excavation of sand also has huge impacts on the structural integrity of buildings that are located near these excavation points. When a foundation no longer has enough grip, roads, bridges, and multistory buildings lose their structural support and collapse.
2. Water availability concerns
Concrete also uses a lot of water during its production process, almost 2.5 liters of water for every kilogram of concrete produced. Right now about 10% of the world’s industrial water use goes toward concrete production; this does not take into account the water used later on the building site. In the next 35 years, an expected 590–710 cubic kilometers of water will be needed to make concrete, if these production methods remain the same. This is roughly equivalent to all the water that flows through the Nile in eight years. Concern for the availability of water resources has increased in recent years as withdrawal in some regions exceeds naturally renewable resources.
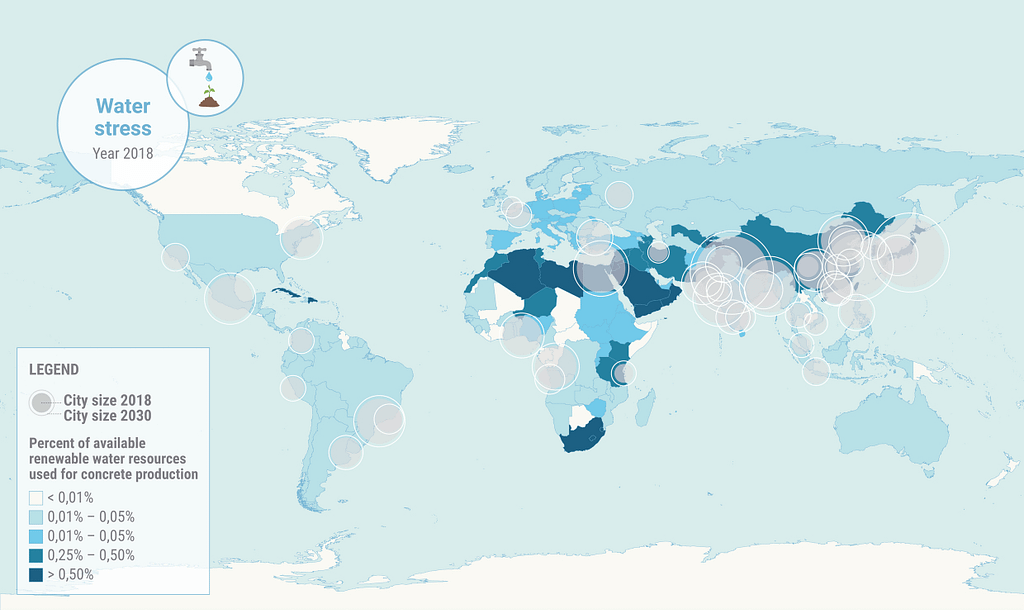
Large swaths of our megacities are situated in water-stressed regions, meaning the increasing need for drinking water and irrigation for food production will compete with the needs for concrete production. It is projected that almost 75% of concrete-related water consumption will take place in water-stressed regions in the year 2050.
3. Climates and contexts
Using concrete and prefabricated building elements leads to very similar buildings all around the world. This uniform type of building (glass skyscrapers) relies less on their spatial conditions (climate) and more on technology to create pleasant interior climates. By doing so we are forgetting centuries of vernacular architecture that have created buildings suited to local climates and contexts.
This leads to the Urban Heat Island effect (UHI), which is a manifestation of contained heat in urban areas, based on human activity (heating, ventilation, air conditioning, commuting, transport) and the accumulation of heat in mineral materials (concrete, masonry). The long retention of this warmth causes cities to heat up over time, negatively affecting air quality, livability, and human health.
Letting go of an old friend: How to build smarter
Continuing with current production and building standards, cities will be hotter, more polluted, dry, waterless, and concrete — not the environmentally sound and picturesque city we had envisioned. To create a more sustainable and resilient future, we cannot keep using concrete the way we have been. If we think differently about the properties of concrete, we can use the material to its advantage, while also making different choices for the development of our cities.
1. Design for longevity
As anyone familiar with the Greek Pantheon (27 BC) in Rome knows, concrete has a long technical lifespan so if we are to use this material, let’s use it to its fullest potential.
In the Netherlands, houses have an average lifespan of 50 years, and offices up to 70. Using materials that have such a massive impact on the environment but can last centuries is not responsible for these projects. One way to tackle this problem is to design for longevity. A great example of this is Dutch architect John Habraken’s ‘open building principle,’ which views buildings as long-term assets. This means they should be able to adjust to technologies, social patterns, and preferences (of the individual and the community).
In 2008, Japan passed new laws incorporating this theory, the 200-year housing concept. Regulatory and administrative tools allow local building officials to evaluate and approve building projects. In exchange for a 200-year lifespan, approved projects receive a reduced rate of taxation. The construction of these projects must be sturdy (perfect for concrete), and all elements must be easily detachable.
2. Lengthen the lifespan of the material: Design for disassembly
If we want to be able to reuse materials and components at a high value, we should design buildings so that this is ultimately possible. Here the ‘Design for Disassembly’ (DfD) framework comes into play. This framework focuses on how different components are connected (something glued is more difficult to remove from a building in one piece than something bolted or screwed), the geometry of the component (other parts of the building should not be ‘in the way’ when removing a component), and the type of materials used (if toxic materials are used in a component it’s not a good idea to reuse them as you perpetuate the lifecycle of toxic materials).
The DfD framework can be used alongside Brandt’s Shearing layers of change, which indicates the different lifespan of building layers and how long certain materials can be part of a building before being replaced. These two frameworks can help designers ensure the materials they use now can be reused in the future.
3. Reuse what’s in the system: Urban mining
When designing, we can consider using materials that already exist in our system. In the Netherlands, a lot of concrete that is removed from buildings is crushed and used as a foundational layer underneath roads. This is not the best way to reuse this material, and is a form of ‘downcycling.’ Instead, we could harvest concrete from the built environment and find a high-value purpose for it. This means we can reduce the need for new concrete, CO2 emissions, and our impact on the environment.
4. Replace with sustainable materials: Regional and biobased
Just working with recycled materials will not be enough to build a more sustainable city. Based on research by Metabolic and the EIB, urban mining can facilitate roughly 30% of the materials needed to build the cities of tomorrow. We will also have to replace concrete with other materials, which requires a local and typology-oriented approach. To create a resilient future where buildings are adapted to local climates and environments, a ‘one size fits all’ solution will not work. Materials that might be sustainable in Canada will not offer a solution in South Africa, and materials for high-rise buildings might not be the best option for social housing. Working with a diverse set of materials and construction methods will strengthen the building stock overall.
Towards a sustainable future
Transitioning from concrete to more sustainable materials is not without obstacles or difficulties. Over the last century, many people have become dependent on the concrete industry for their livelihoods. With more than 13% of the world GDP connected to the building sector, an overnight overhaul will have massive implications and is not reasonable. As we transition, we must also be wary of burden-shifting, considering for example all the nature that might be destroyed. Cutting down forests to produce additional lumber, without a clear replanting strategy, will not bring about the sustainable future we want.
By 2050, when I open my window, I truly believe I will look out onto the sustainable and healthy city we have envisioned. However, the first step is to make rigorous changes to the way we design and build our houses. Fully understanding the environmental impacts we are creating along the entire production chain will then inform a solid transition strategy. There is a path lined with eco-friendly and local materials to build the sustainable megacity of tomorrow — let’s be brave enough to take it.
As we rethink how to build our cities without concrete, let’s explore alternative materials that are being used successfully around the world:
Material: Wood
Location: Norway
Mjösa Tower (Mjøstårnet) is an 85.4m-tall mixed-use timber building in Norway. It has 18 floors and includes a hotel, private homes, and office spaces. It is the third tallest building in Norway and has been credited as the tallest timber tower in the world by the Council on Tall Buildings and Urban Habitat.
Nearly the entire building is made with locally produced cross-laminated timber products. Only on the top seven floors have 30 cm of concrete incorporated into the deck to improve the strength of the building and to prevent it from swaying in the wind. Steel plates and dowels are used to connect all structural elements of the tower.
In total, the building contains 2,600m³ of wood.
Material: Compressed Earth Blocks
Location: Senegal
Unlike traditional bricks that require baking, compressed earth brick is unprocessed, unbaked earth and sand that is slightly moistened, compressed, and dried. Added vegetable fibers can improve technical requirements for structural stability of insulating characteristics. The resulting bricks are strong enough to create walls and structural elements. Since these bricks are not processed or baked, they have a very low energy footprint.
The porous blocks help to regulate the relative humidity of a space, creating a healthy living environment. The high density of the soil buffers the heat during the day and releases it at night. It also contributes to the acoustic and aesthetic comfort of the home. Finally, the soil is fire-resistant.
Compressed earth blocks are a reproducible and universal technique that can create jobs for unskilled labor. Building with raw earth makes it possible to use local materials. The use of soil is compatible with other materials and techniques (wood framing, prefabrication, block construction, etc).
Buildings made with compressed earth (blocks) are found all over the world and can be hundreds of years old. Examples of this construction method have been found in China, Iraq, Yemen, France, Belgium, and Spain.
Material: Bamboo
Location: Asia and South America
Bamboo is commonly used as a building material in regions where the climate is best suitable for its cultivation, such as (Southeast) Asia and South America. With the right conditions, bamboo is one of the fastest-growing plants in the world due to its horizontal underground stem growing system.
Often used as a support structure for concrete and as construction scaffolding, bamboo is still widely used for bridges, structures, and houses. Bamboo is well known for having almost twice the compressive strength of concrete and almost the same strength to weight ratio as steel in tension forces, which is why buildings made of bamboo are resistant to wind and earthquakes. However, the question remains if this material is long-lasting.