Imagine, for a moment, an architect.
She is environmentally conscious in her lifestyle choices, but there is one area where she struggles to make an environmentally conscious choice: her work. Whatever building she designs, however energy efficient it is—double-pane windows and shades that raise and lower automatically with the movement of the sun—she is limited in the amount of recycled materials she can design into her building.
The reason is a lack of data.
Metabolic consultants have been working to close this gap. With the right data, they are finding it’s possible to catalyze activity in areas of the economy that need to be made circular in order to meet climate targets such as those set forth in the Paris Agreement, as well as more particular and local environmentally-related goals set by companies, sectors, and governments.
Take construction and demolition as an example. Recent years have seen an increase in interest in what has been called urban mining: sourcing materials for construction and manufacturing from cities, where 75% of resources are concentrated on 3% of the world’s land. Think of it as recycling on the municipal scale: By increasing the amount of materials that is reused, we reduce pressure on natural environments to provide them anew, and extend the sustainability of resources so we don’t run up against planetary boundaries.

Adapted from ‘Circle Economy – Master Circular Business with the Value Hill’ (2016)
In the Netherlands, municipalities must reduce their primary materials usage 50% by 2030 (and fully circular by 2050). With a widely-acknowledged housing crunch, however, it can’t just stop building. Yet new construction and even conversion stimulate high demand for construction materials, which are typically of primary origin. So our architect will need to make more use of reused and recycled materials—she will need to be able to mine the urban environment.
“Clients ask us, ‘Okay, we need to use more recycled materials,” says Metabolic consultant Martijn Kamps. “Architects are aware that a lot of these materials are stored in the built environment. But they don’t really know how much there is or what the quality is, and how much they can recycle in order to meet their sustainability targets.”
The architect can’t design an apartment block or an office building—in the Netherlands or virtually anywhere else—to make use of the urban mine because she doesn’t know when or where reusable or recycled materials will be available.
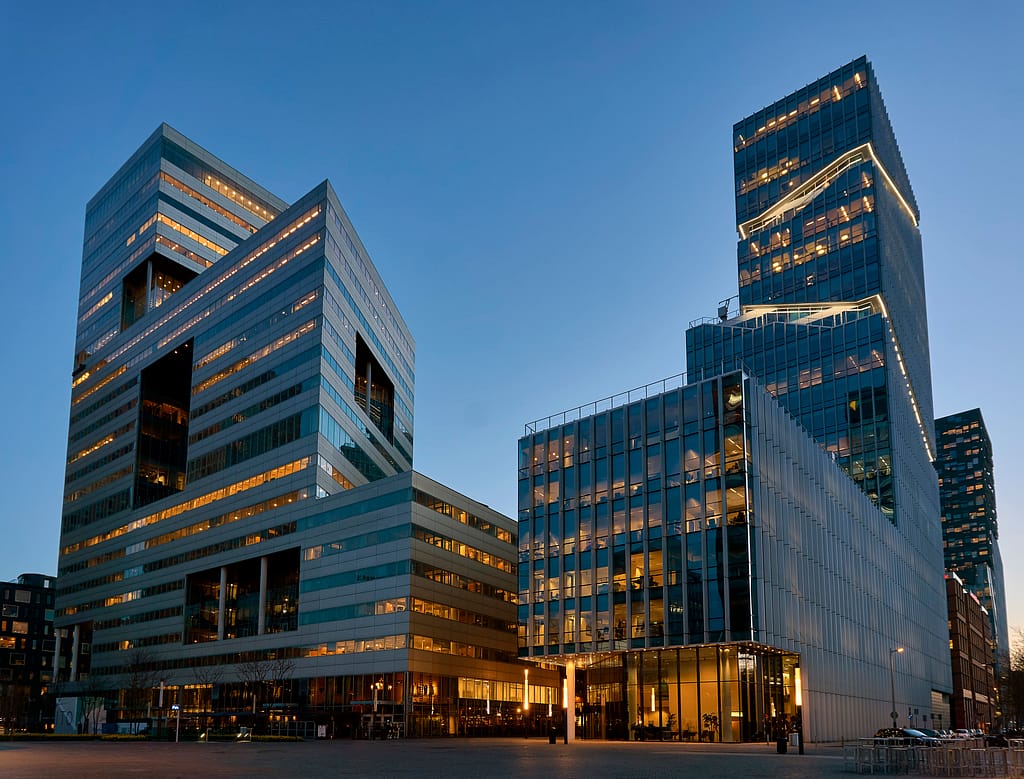
But if she had data on the availability of reusable or recycled materials, she could incorporate those into her design, enabling her and the construction industry as a whole to use such materials in situations where they had not been able to previously—while creating a market for the recycled material, which incentivizes both its collection and the tabulation of data about it.
“In the last couple years, we’ve created models of increasing complexity that help governments and construction or demolition companies to assess how much and what quality of materials are stored in buildings across a city,” says Kamps. “By mapping the demolition projects we can model the materials that will be released from the built environment and are available for re-use.” In October, he presented his findings to the environmental management program at the National University of Singapore. (Kamps himself has a master’s in environmental management from the University of Amsterdam.)
Kamps found that gaps exist in data pertaining to both time and space. Our architect needs to know in advance what materials will be available that she can use in her planning and design process. If she were to know that 500 wooden doors from a demolished hotel will become available, newly refurbished, two months before the client wants construction to begin, she could contribute to progress on the primary materials reduction mandate.
The location gap pertains to the environmental feasibility of transporting materials. At a certain point, it’s more efficient to make a product new than to transport it some distance. Concrete or steel, with their high energy inputs for manufacture, can be moved farther than wooden doors before running into this limit.
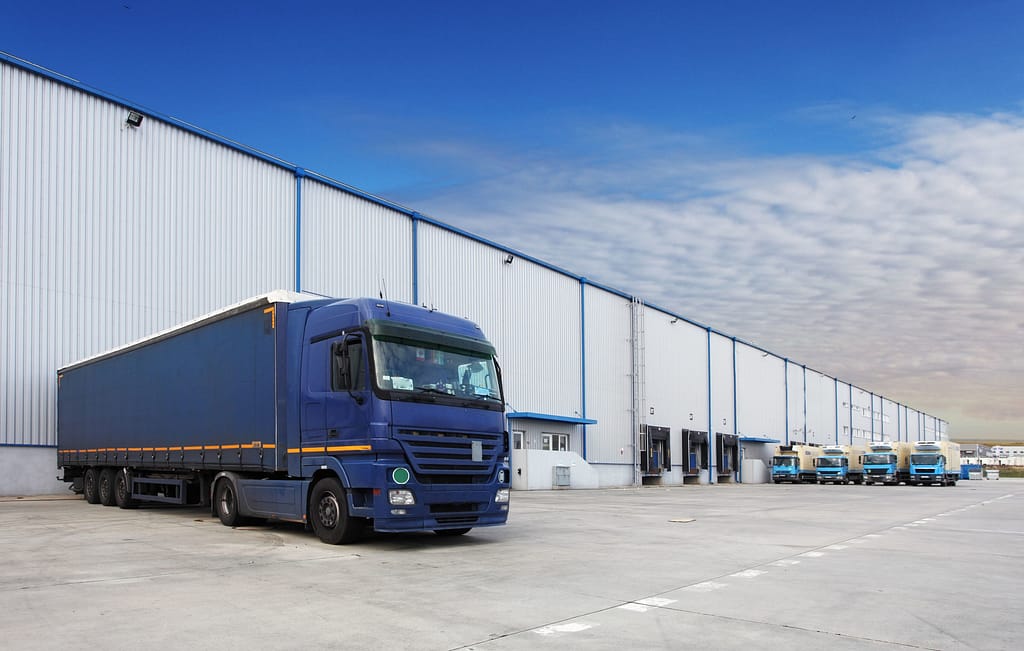
Kamps envisions cities requiring, as part of the permitting process for demolition, an assessment of materials that will be available afterward and plans for what to do with them. That information—and, later, the material itself—would go to a city warehouse that stores the materials between demolition and refurbishment, and between refurbishment and re-use. Cities could further contribute to their waste-reduction goals by requiring circular procurement of materials in their tendering criteria for municipal projects.
By contrast, current models take a top-down approach: estimating what materials will be available when, based on when buildings were constructed, their function, size, and information from the municipality on when which buildings will be demolished (or estimated lifespan based on the local real estate market and other factors, if such records are unavailable).
“We estimate the materials that will be available in the coming years in which areas,” Kamps says.
“Ideally, you would do these calculations every year for every municipality, so you know how much materials will be available and where. Then, depending on the type of material, you’ll need urban mining hubs, where you can store and process these materials before they can be reused.”
The need for hubs indicates an important part of Kamps’ process. “Cities need to have the physical space to store and process these materials, so it needs to be part of their zoning,” Kamps says. He and colleagues mapped the material flows of construction and demolition waste in Rotterdam to determine where demolition projects occur, and which materials will be available and when. Reuse being preferable to recycling—value is often lost in recycling, and it burns energy—it was also necessary to model building elements. This process matched supply (demolition projects) and demand (construction projects), showing the sum of building areas and the amount of materials required.
By increasing the amount of materials reused or recycled, builders decrease the amount of primary materials needed and, by extension, resources extracted. Environmental impacts are thereby reduced—if fewer new wooden doors are needed, perhaps less forest can be demolished, potentially limiting biodiversity loss, increasing water retention, and retaining soil quality.
Rotterdam was only the beginning. Metabolic has since mapped the urban mines of Amsterdam and all of the Netherlands, and taken its expertise overseas, to Philadelphia. We are now engaged on a project for the Joint Research Commission, the research branch of the European Commission, to calculate all materials currently in all the buildings of the EU. Consultants including Kamps will be looking at emerging technologies to process and recycle these materials.
With that, perhaps, the architect can reduce her footprint more than she imagined possible.